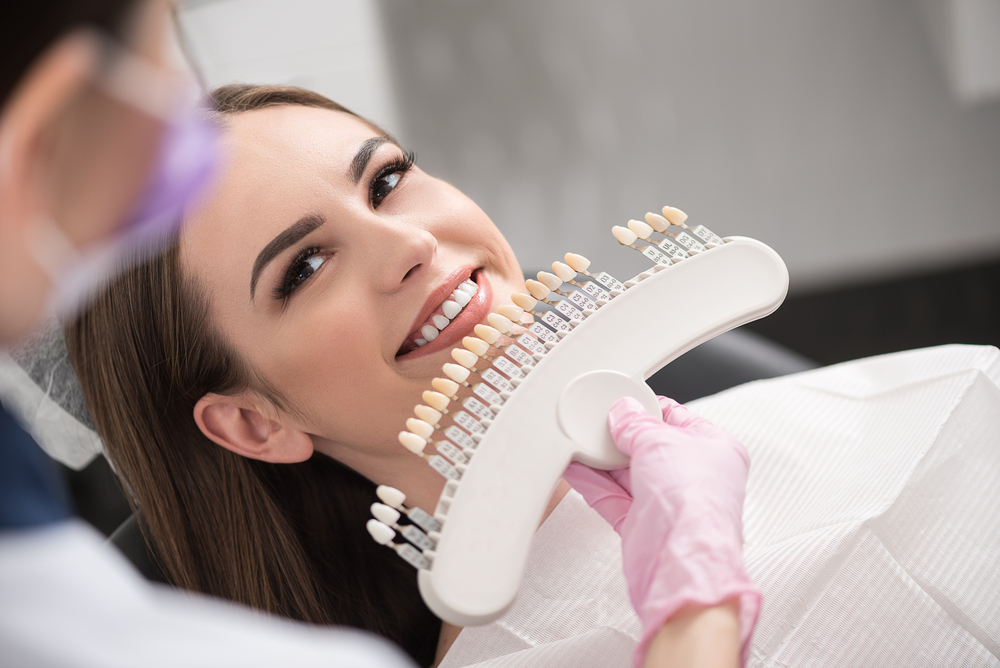
3D Printing and the Dental Crown Manufacturing Process
Core to restorative dentistry, dental crowns are used to protect worn or broken teeth, cover dental implants, anchor dental bridges, and complete root canal procedures. Over the last three decades, digital workflows have gradually replaced traditional methods. With higher accuracy, speed, and more consistent results, modern dentistry manufacturing processes are the preferred choice.
In the past, digital workflows used a combination of CAD/CAM software and CNC milling to make crowns. 3D printers could not make permanent crowns because the materials did not have the appropriate mechanical properties, and there was poor accuracy or fit. With recent advancements in 3D-printable resins, 3D printers can produce permanent crowns that meet mechanical property requirements and make them faster and more cost-effectively than CNC milling. 3D printing is streamlining the dental crown manufacturing process and can benefit labs and dental practices.
Why Dental Technicians are Shifting to Digital Crown Production
Dental practices manufacture crowns in two ways: outsourcing or in-house production. In the outsourcing model, the dentist sends a patient’s oral impressions to a dental lab. There, the crown is fabricated and sent back to the practice. The process takes around three weeks to complete. With in-house production, dental practices significantly shorten turnaround time. Depending on the materials and 3D printing machine, dentists produce a crown in a matter of hours.
Dental labs produce crowns with either analog or digital workflows. Digital is gradually becoming more popular than analog because it can create crowns of equivalent accuracy and durability faster. In-house production at orthodontist offices is exclusively digital, as analog workflows require more specialized tools, materials, and labor steps to produce parts.
How 3D Printing Differs from Other Dental Crown Manufacturing Processes
3D printers produce crowns faster and with fewer labor steps compared to traditional manufacturing or CNC milling. Dental labs and private practices can adopt 3D printers to more efficiently fulfill orders and are ideal for dental crown production based on several factors:
Material Accuracy and Price Point
The dental resins used by 3D printers are durable—resistant to daily wear, easy to work with, and safe for extended oral exposure. Crowns made with 3D-printable resin meet all mechanical property requirements and have the look and feel of real teeth.
Crowns made through traditional means are unable to match the accuracy of 3D-printed crowns. The numerous labor steps and materials used in methods like lost-wax casting make analog crowns highly susceptible to human error. A comparative study shows that 3D-printed crowns are more accurate than crowns produced through more manual means.
A separate study reveals that 3D-printed crowns are also slightly more accurate than milled crowns. Labs typically make milled crowns with ceramic materials. 3D-printable resins are more affordable than ceramic and have high strength and durability.
Time to Make
3D printers create crowns at a faster rate than other production methods. Using traditional processes, it can take weeks to produce a single crown. In recent decades, labs and practices have turned to CNC milling to reduce this turnaround time from days to hours. Now, 3D printing offers a way to take CNC milling’s digital workflow and make the process more efficient.
3D printers create crowns using the same CAD/CAM software found in a CNC milling workflow, but they can produce crowns in a shorter time frame. CNC machines also require significant setup time, whereas 3D printers do not. The time-saving capabilities of 3D printers allow dental labs to meet large orders easily and for private practices to provide better customer service. 3D printing’s fast turnaround also makes it ideal for lower volume production, while recent advancements in 3D printing technologies, digital workflow, and materials have made high-volume production possible as well.
Simplified Workflow
The traditional crown manufacturing method is an artisanal process that requires significant hands-on work. Typically a practitioner takes patient dental impressions and sends them to a lab. Next, a lab tech makes a mold, heats, cools, and polishes the metal, ceramic, or composite to form a wearable crown. With digital workflows, there are significantly fewer steps in the dental crown manufacturing process, and it is more accurate and repeatable.
In a digital workflow, the dentist takes digital impressions of the patient’s teeth using an intraoral scanner. The files are processed using dental CAD software, and a model file exports as an STL file. If the digital workflow uses milling, a tech needs to convert the CAD model, mill the crown and perform various material-dependent post-processing steps to achieve the desired durability. The crown is then ready for placement in the patient’s mouth.
3D printing enables lab techs to simplify the digital workflow by replacing the labor-intensive aspects of dental crown post-processing. Preparing a milled crown for placement requires a combination of sintering, crystallization, glazing, and cooling, depending on the material. Techs simply remove the supports, wash, cure, and polish the 3D-printed crown before it is ready for the dentist to put in a patient’s mouth.
How to 3D Print a Dental Crown
3D printers allow dental labs and practices to create solid and accurate crowns for their patients. The workflow is easy to learn and adopt. Here the process is broken down into four steps:
1. Scan
The dentist collects anatomical data of the patient’s mouth by using an intraoral scanner. The dentist either sends the file to a dental lab or uploads it to their in-house system.
2. Design
A tech imports the scan into the software and trims the scan to remove unnecessary data and select the portion they’ll print. The tech then generates support points for the model and exports the file to the printer.
3. Print
The tech prepares the printer by inserting the resin tank, the resin cartridge, and the build platform. They begin printing by selecting the appropriate file on the printer’s menu. Following a series of prompts and dialogs, the printer will automatically start building the crown.
4. Prepare
After the crown prints, the tech removes the build platform and places it into a wash. Following a manufacturer-specified amount of time, the tech inspects the parts for any uncured resin on the surface. If any resin remains in between the supports and rafts, the tech uses an isopropyl alcohol-filled squeeze bottle and brush to remove it.
The tech uses compressed air to dry the crown. Once dry, the crown is removed from the platform and placed into a curing box. After a manufacturer-specified amount of time, the crown is removed from the curing box, and the tech removes the support structures. The crown is checked for accuracy, contoured as needed, and cured again.
After the second curing, the crown is ready to be placed.
3D Printers Improve the Dental Crown Manufacturing Process
3D printers enable dental labs and dental practices to digitize workflows for more efficient production. By introducing 3D printing into operations, labs and practices can make crowns that are more accurate and affordable than other production means. There are multiple types of 3D printers that can meet different business model requirements.
Industrial printers like the Lux3 have the power and build-platform to meet large dental labs’ production needs. Private dental labs will benefit from Luxadent, a desktop 3D printer specifically made for dental applications. The Luxadent is compact, affordable, and still has all of the capabilities of the Lux 3. Both printer options have full access to LuxCreo’s line of dental resins. Amongst the available offerings are materials built to make:
Call today to inquire about our dental printing solutions and experience first-hand why 3D printing is the future of dentistry.
To learn more about the dental crown manufacturing process, visit our contact page or call (650) 336-0888.