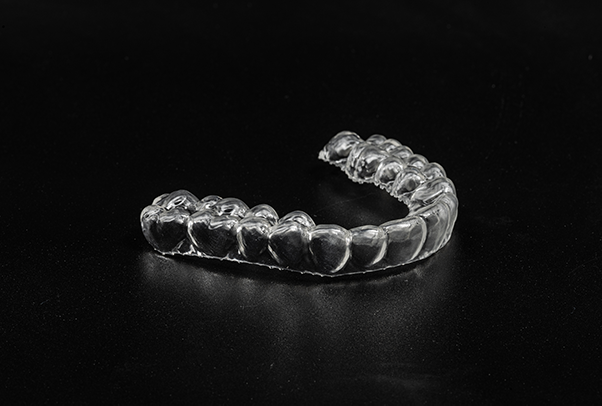
The Benefits of 3D-Printed Orthodontic Retainers
Removable retainers are the most commonly prescribed retainers today, with nearly 60% of orthodontists preferring them over fixed lingual models. The conventional process to develop removable retainers is an outsourcing model. It takes weeks to complete, necessitates multiple patient visits to the practice, and requires the uncomfortable step of taking impressions to make oral molds. 3D printing technology improves the retainer creation process by accelerating product turnaround time, eliminating the need for dental molds, and allowing orthodontists to produce retainers in-house.
Practices that incorporate 3D-printed orthodontic retainers into their operations experience the following benefits:
Better Customer Service through Faster Turnaround
3D printing is an efficient production method with extensive customization capabilities. Early 3D printers were too large, slow, and expensive for private practices to afford, but hardware advancements have removed those barriers. Today, dental professionals have access to affordable and compact 3D printing solutions that develop retainers, clear aligners, and other oral devices that are faster than other production methods. Solutions like LuxaDent and iLuxPro Dental achieve fast turnaround times by directly printing appliances with transparent materials—a previously impossible task.
Orthodontists and labs initially used 3D printers to create dental models for thermoforming, as it was not possible to print appliances directly. When direct printing became possible, the extensive buffing and polishing required during the post-processing stage contributed to the total production time—taking per batch—approximately 2-3 days with SLA or 3 hours with most DLP printers. The post-processing steps also require heavy equipment and a dedicated room. Now, advancements in better resins, 3D printing technology, and resin-printing techniques are eliminating many post-processing steps, allowing orthodontists to produce clear retainers in 1 hour per batch on a desktop 3D printer.
The accelerated turnaround time of transparent printing with modern 3D printers is transforming practices by enabling same-day services.
A More Sustainable Production Process
The direct printing of clear retainers removes most of the material waste with conventional retainer production. The traditional process entails:
- Developing oral impressions by placing dental trays with alginate into the patient’s mouth
- Filling the oral impression with a mixture to develop a dental mold.
- Thermoforming a heated thermoplastic sheet over the mold to shape the retainer.
- Removing the cooled retainer from the mold
- Cutting off the excess plastic from the retainer
- Buffing and polishing the retainer
When a technician finishes a retainer, the impressions, molds, and excess plastic are discarded. Through direct printing, 3D printers eliminate the need for thermoforming as well as related waste.
3D printers use digital files to guide production instead of physical dental models. When outsourcing, the orthodontist sends the digital files of the oral scan to either a dental lab or a 3D printer-filled smart factory—a more efficient option than shipping the mold. At the lab or smart factory, the technician prints the retainer with a defined gum edge already in place, eliminating the need for trimming. The only excess material is the small dimple contacts along the support structure that can be buffed out in minutes.
Orthodontists that use in-house 3D printers maximize sustainability by removing transportation requirements as well as significantly reducing waste.
Increased Patient Comfort
3D printers support a more comfortable patient experience for retainers by replacing oral impressions with digital with intraoral scans. Creating physical oral impressions is invasive and unpleasant for patients, as the plaster-filled trays cause gagging and taste unpleasant. Patients respond better to the wands used by intraoral scanners as they limit physical contact.
Legacy 3D printing solutions used digital impressions to create the dental model for thermoforming. LuxAlign, the latest in orthodontic 3D printing software, converts the digital dental model into a 3D-printable retainer file for direct printing. LuxAlign enables faster turnaround time than other retainer production methods and can achieve higher accuracy than thermoforming-produced retainers. The most advanced 3D printers produce retainers that fit better than ones made with thermoforming, currently printing up to 25-micrometer in resolution and allowing exact definition of the gum line. With 3D printing, orthodontists can offer patients a more comfortable experience and deliver higher quality retainers.
Experience The Benefits of 3D-Printed Orthodontic Retainers
Modern 3D printing solutions create better retainers faster than other production methods and require minimal post-processing. Solutions like LuxaDent are transforming the business with same-day aligners, producing retainers in an hour or less and only needing quick buffing of contact points before they are ready to use. Printing transparent orthodontic retainers also increases sustainability by eliminating material for physical oral impressions and dental models and reduces thermoplastic waste. The digital process, from oral scan to 3D printable file, replaces physical oral impressions and provides a more comfortable patient experience with a more accurate and better fitting product.
For those ready to learn more on how LuxCreo’s LuxaDent or iLuxPro Dental printer, LuxAlign dental software, and a suite of dental-specific resins can improve your operation’s efficiency and appliance quality, visit our contact page or call (650) 336-0888.