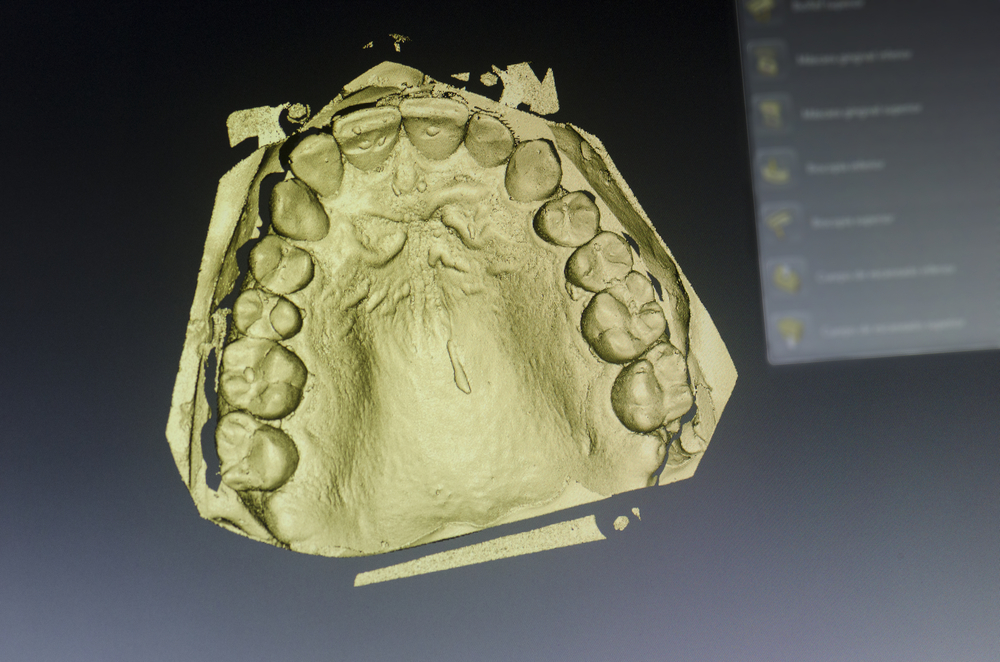
How to 3D Print Dental Study Models
Dental service providers need accurate dental study models to aid diagnosis and treatment planning. Dental study models show patients what they can expect from their treatment plans and are used for fit checks instead of having the patient come back to the dental office. Dental and orthodontic practices require accurate dental study models. However, the traditional manufacturing process is time-consuming, and producing dental models often requires help from a lab.
3D printing has made an impact in numerous industries including dental, manufacturing a wide range of products. With recent advancements in additive manufacturing machines, 3D-printable resins, and 3D printing dental software, practices and labs can use 3D printers to produce dental study models faster than the traditional casting process. 3D printing replaces the many steps in traditional model manufacturing with a fast and easy printing process that yields a more accurate product.
Problems with Production of Traditional Dental Study Models
The traditional process used to fabricate dental study models is time-consuming and requires significant specialized labor to produce an accurate model. After taking a dental impression of the patient’s mouth, the following process is used to create a dental study model:
- Material mix and first pour: The dental stone or plaster material requires thorough mixing to remove air bubbles. A practitioner pours the mixture into the disinfected impression and sets it on a vibrating plate to force the material into the tooth depressions.
- Second stage pour: Next, they mix and pour the second batch of material on a glass slab to produce a base for the study model and invert it onto the base to allow the materials to bond.
- Drying: The stone mixture dries for approximately one hour. Once dried, the practitioner removes it from the impression and the supporting slab.
- Trimming: Once the practitioner removes the dried dental study model from the impression, they trim excess material from the edges using a grinding wheel.
Crucial for diagnosis and treatment planning, the process for making the models is time-consuming, and in some cases the accuracy is insufficient. 3D printing offers a better fabrication process with faster turnaround times, highly competitive costs, and more accurate models leading to better patient outcomes.
The 3D Printing Process for Dental Study Models
The process for 3D printing dental study models is similar to that used for 3D printing thermoforming molds for clear aligners or retainers. A software package like 3Shape or another application creates a three-dimensional digital model from an intraoral scan. The digital model can be directly 3D printed using several methods like stereolithography (SLA) and distributed light processing (DLP).
After printing the study model, it requires post-processing, and the required labor is much less than traditional production methods. Different 3D printing materials and processes generally have differing post-processing requirements. Advanced 3D printing solutions, such as DLP with dental model resin materials, require minimal trimming and washing treatment after the resin cures and produce a highly accurate dental study model with longer shelf life than ones made from dental plaster or dental stone.
The curing time for resins is much shorter than dental plaster or l stone, speeding up the overall production time. In addition to reduced time, the automated process to produce a dental study model with 3D printing involves minimal labor and is more accurate – improving the accuracy of a diagnosis, streamlining treatment planning, and providing a better patient experience.
How to Access 3D Printers for Dental Study Models
While there are numerous benefits to additive manufacturing including an accelerated process, not all 3D printing solutions can produce high-quality results.
Dental professionals can reduce their production time without increasing operational costs when using the right dental 3D printing solution. Advanced 3D printers that use FDA-approved resins are an ideal solution for producing accurate dental study models, nightguards, clear aligners, surgical guides, and other appliances. When you work with the right 3D printing partner, you can bring these capabilities in-house, outsource to a dental lab, or access 3D printers in a remote facility via the cloud.
LuxCreo’s patented LEAP™ (Light Enabled Additive Production) process enables outsourced or in-house 3D printing of dental study models with high performance and quality additive manufacturing materials. We offer cloud-connected 3D printers with on-demand production in a Smart Factory for rapid prototyping or full-scale production. For more information on how our services can improve your supply chain and manufacturing processes, visit our contact page or call (650) 336-0888.