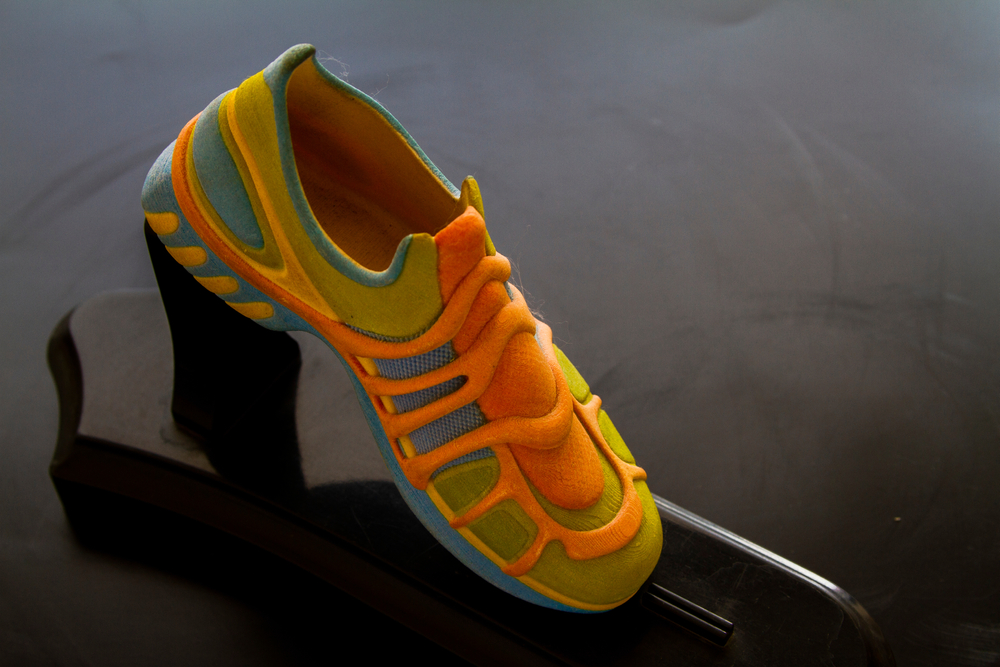
Footwear Manufacturing Industry Analysis: Evaluating the Impact of 3D Printing
By the end of 2020, the total revenue connected to 3D printed footwear production is projected to reach $1.4 billion, an upward trend over the last few years. According to a recent footwear manufacturing industry analysis, it is expected to grow at a 19.5% CAGR to $6.5 billion by 2029.
Final parts such as uppers, insoles, and midsoles make up 34% of 3D printed footwear revenue, and by 2029, expected to increase to 54%. Leading the growth are midsoles. Footwear companies are leveraging additive manufacturing technology to improve final product performance and create localized and personalized products.
Listed below are four 3D printed footwear applications and reasons they will grow over the next decade.
Midsoles
3D printed midsoles significantly impact the footwear industry and are the fastest-growing application of additive manufacturing in consumer footwear. In 2019, a major footwear manufacturer introduced over 100,000 shoes outfitted with 3D printed midsoles into the market. Numerous other footwear companies also made announcements on leveraging 3D printing in upcoming years.
Injection molding produces midsoles at high volumes. However, it also creates a lot of waste and does not allow for customization or personalization. Most midsoles are made of ethylene-vinyl acetate (EVA) foam and degrade faster than 3D printed polyurethane polymer materials. 3D printing midsoles have two considerable advantages over injection molding:
- Longer Lasting Materials: EVA foam is lighter than polyurethane. However, on average, shoes constructed with EVA foam midsoles start to experience compression long before 100,000 heel strikes. Once there is compression, the shoes steeply decline in both performance and comfort. Leading 3D printed materials are significantly longer-lasting, withstanding more than 1,000,000 heel strikes before experiencing degradation in the rebound.
- High Customization: 3D printing allows manufacturers to optimize the midsole structure to accommodate a broader range of individual customer preferences. Flexibility, weight, and fit can all be adjusted to give consumers a shoe that performs as desired. For runners, customization improves track performance as the shoes provide support and resilience tuned to the athlete’s body.
Major athletic footwear companies are using 3D printed midsoles to create high-performing and longer-lasting products.
Personalized Uppers
Making shoe uppers is labor-intensive. They require workers to cut, stitch and glue multiple parts together to create a piece that is then glued to the midsole. 3D printing often produces midsoles, but an industry analysis in footwear manufacturing shows that major companies are starting to apply additive manufacturing, improving the process to manufacture uppers.
One method involves consolidating different upper parts into a single design—the upper prints with a flexible plastic such as thermoplastic polyurethane (TPU). By simplifying the design, manufacturers eliminate assembly steps, simplifying the production process. A 3D printed shoe can also be more durable. Fusing 3D printed layers eliminates the friction found with woven or knit textiles.
A 3D printed shoe can last longer knitted, and many consumers prefer woven textiles. Leading 3D printing companies are looking at leveraging 3D knitting in 3D printing. 3D knitting is another form of additive manufacturing that uses automated methods to weave fabric into a seamless apparel piece. As 3D printing resolution improves, it will print fabric—enabling footwear companies to customize the entire shoe.
Limited Edition Production Runs
Conventional footwear production methods constrict design freedom as it requires expensive and often time-consuming retooling for significant design changes. With 3D printing, digital design files can be easily altered and produced. Free from the tooling limitations, footwear manufacturers can leverage 3D printing for cost-effective, low volume production runs.
Potential applications of 3D printing for limited production runs:
Customized designs | Meet individual customer mechanics, similar to the advantages outlined in the midsole section. |
Personalized aesthetics | Greater level of alterations in structure, graphics, texture, and color than traditional manufacturing |
Fast production | Capitalizes on trends at a swift pace while still maintaining sustainability. |
Rapid Prototyping
3D printing’s ability to quickly produce materials at a low volume also powers fully functional prototyping [Live link: ” What are the Current Trends in Additive Prototyping?”], which can bring footwear products from a sketch to production-ready in under a month, or even faster.
Customized Orthopedic Insoles
Traditionally, orthopedic inserts require significant hand-crafted work. Podiatrists make an impression of the patient’s feet using a foam box to create a 3D mold or applying plaster to the feet to create a slipper cast. The 3D model is then adjusted further to align with the patient’s foot. Once the cast sets, the podiatrist chooses a combination of materials that are most appropriate to fit the patient’s needs. The materials would be vacuum-pressed over the cast to form a shell. The shell is then trimmed, ground, and fitted to the patient’s foot.
3D printing improves the process in a variety of ways. Digital scans are taken of the patients’ feet. The 3D models created from the digital scans are more accurate and less labor-intensive than a mold or cast. Specialists take the digital models and print them using a single material that can be adjusted using geometry to achieve patient requirements, eliminating multi-material construction. The removal of hand-crafted work and material consolidation enables specialists to make insoles faster and at a lower cost than traditional methods.
Our Footwear Manufacturing Industry Analysis: 3D Printing is on the Rise
Studies show that revenue from 3D printed footwear will continue to grow. Companies are already implementing additive technology to provide higher-performing footwear. With greater design freedom and agility to meet market demands, 3D printing will enable broader support of limited edition products and customized midsoles.
To learn more information regarding footwear manufacturing industry analysis, visit our contact page or call (650) 336-0888.