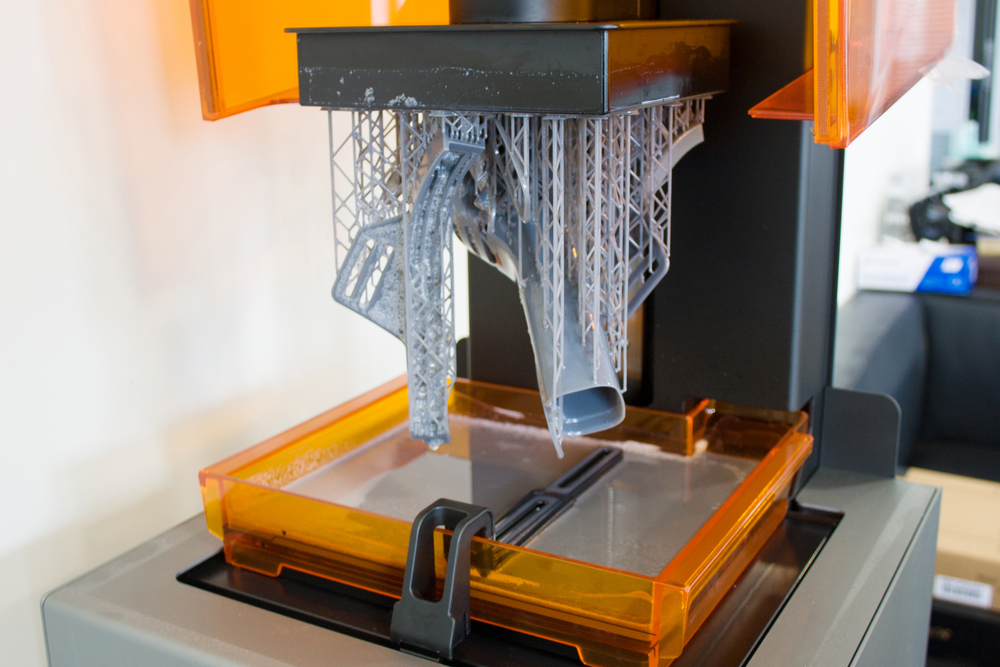
Additive Manufacturing vs. Traditional Manufacturing: High-Volume Production
For many years, no one considered additive manufacturing as a scalable method for high-volume production because older 3D printing systems did not offer high throughput, had poor surface finishing, and inadequate material properties. Additive manufacturing is 3D printing on an industrial scale. In high-volume 3D printing, multiple production lines with high-throughput processes are used to produce a range of products. Today’s advanced 3D printing solutions with advanced materials, faster speed, and higher throughput allow companies to take a hybrid or fully additive manufacturing approach. The flexibility of a single 3D printing process to produce a range of products is helping many companies transform their manufacturing and business models to become more efficient and agile as well as better mitigate against supply chain disruptions.
Conversely, traditional manufacturing lines can only produce a single product or a low mix of very similar products at high volumes. Traditional manufacturing processes, like injection molding, require a different product design and production approach compared to additive manufacturing. When examining differences between additive manufacturing vs. traditional manufacturing, companies need to evaluate current technologies as rapid innovation in 3D printing is enabling companies to produce finished products with very little post-processing.
Comparing Additive Manufacturing vs. Traditional Manufacturing
Additive Manufacturing
All high-volume implementations of additive manufacturing rely on a high-throughput 3D printing process that can fabricate products with accuracy to meet product specifications. Many materials used for 3D printing can compete with their traditional counterparts in terms of material strength and durability. With the ability to produce more complex parts, 3D printing can enable the consolidation of multiple parts into a single piece, reducing or eliminating assembly to produce the final product.
Popular 3D printing processes used in additive manufacturing include:
- Material extrusion (FDM or FFF)
- Powder bed fusion (PBF)
- Directed-energy deposition (DED)
- Binder jetting
- Sheet lamination (LOM)
- Vat photopolymerization (SLA or DLP)
- Selective laser sintering (SLS)
Some industries that currently use 3D printing processes include aerospace, robotics, medical, dental, and footwear, and other consumer goods. Recent advances in DLP 3D printing processes enable high throughput and printing resolution. Supporting larger build platforms, multiple designs can print in a single batch with the vat photopolymerization process.
The major advantage of additive manufacturing is that it does not require tooling, making it flexible to produce a broad range of products. With advancements in 3D printing systems and materials, manufacturers can directly print finished products with minimal post-processing, reducing material waste. The printable product size and throughput are correlated to the build volume in a 3D printer. Newer printers can print much larger products or support a high mix of multiple products in a single batch.
Traditional Manufacturing
Traditional manufacturing processes require the development of specific tools and are only cost-competitive with high-volume production. Common traditional manufacturing methods are:
- Injection molding
- CNC machining
- Plastic joining
- Plastic forming
Up-front tooling costs for traditional manufacturing processes are amortized across production runs. With very high volumes, the cost per unit can be significantly minimized. T However, traditional processes tend to have high material waste and often require additional assembly for products that have anything more than a simple design. With the traditional process, there are many challenges to producing customizable, one-off/limited run, or complex products as well as ensuring the final manufactured product is aligned with the approved prototype design.
How Additive Manufacturing Complements Traditional Processes
A single 3D printing machine easily produces a range of products without tooling and can quickly scale up into a full-fledged additive manufacturing operation with multiple machines. The choice between additive manufacturing vs. traditional manufacturing does not need to be binary. Additive manufacturing can complement traditional processes in several ways including:
- Part consolidation: Additive manufacturing can produce highly complex products. A complex part that is produced as multiple smaller pieces with traditional manufacturing can 3D print as a single part without requiring assembly. It may be more efficient to 3D print complex parts even at high volume while manufacturing simpler parts with traditional production methods.
- Flexible production capacity: Some products have unpredictable demand, and companies can use 3D printing to augment production capacity to respond to demand changes – supporting multiple products. Companies can take an agile approach to production and distribution rather than holding and managing inventory.
- Accelerating prototyping: 3D printing speeds up prototyping, helping design and engineering teams evaluate the functionality and aesthetics of a new product. Using 3D printing, teams can more easily produce multiple prototypes in a single batch to experiment with design choices. The finalized design can then be produced at scale with a traditional process or a combination of both methods.
Manufacturers that want to implement a fully additive manufacturing process or complement traditional processes need to work with a 3D printing solutions provider that focuses on industrial-scale additive manufacturing. The right provider can help traditional manufacturers by connecting local 3D printers at a site with a 3D printing smart factory. Alternatively, companies can bring 3D printing solutions in-house and integrate them into traditional manufacturing operations to enable agility, less material waste, competitive production costs, and reduce product complexity.
If you’re looking to use additive manufacturing vs. traditional manufacturing for your products, LuxCreo provides advanced 3D printing solutions that use their patented LEAP™ (Light Enabled Additive Production) technology. LuxCreo’s smart factory-connected 3D printers help you access on-demand production at a 3D printing smart factory. For more information on how our services can improve your supply chain and manufacturing processes, visit our contact page or call (650) 336-0888.