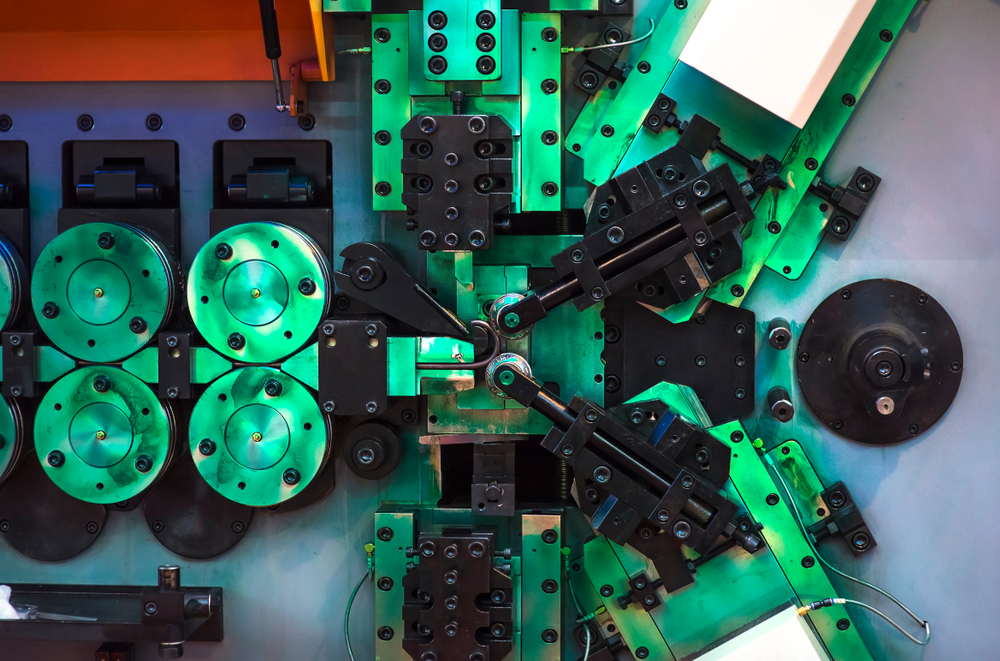
3 Advantages of 3D Printing Over Traditional Manufacturing
3D printing has matured significantly since it was introduced in the 1980s. Advancements in 3D printing are enabling companies―in a broad range of industries―greater flexibility in promoting ideas into production. Innovations such as high-performance materials and shifts from tracing to projection printing have significantly elevated the advantages of 3D printing.
3D printing is often perceived as slower and more expensive than traditional production methods. Many companies incorrectly assume it to be inaccessible because it’s different and more complex. However, improvements in 3D printing technologies and increased material performance have made additive manufacturing a viable alternative. Increased agility, reduced costs and risks, and onshoring will accelerate product design through production more effectively than traditional manufacturing methods.
Getting a Product Through Traditional Manufacturing vs. 3D Printing
3D printing addresses many of the inefficiencies and challenges in traditional manufacturing methods. Traditional manufacturing processes utilize expensive tooling for production. To overcome tooling limitations, designs must be adapted before high-volume production is possible.
The flowchart below shows how new products move from ideation into full-scale production; comparing traditional manufacturing processes with 3D printing. In traditional manufacturing, products must go through multiple stages of evaluation and adapted to the specific production process before scaling. By contrast, 3D printing allows multiple SKUs to be developed in parallel, and the product won’t need a second round of re-designs before scaling.
Traditional manufacturing often requires multiple design phases. 3D printing eliminates redesign cycles when moving to the high volume production stage and allows multiple SKUs to be developed.
Standard manufacturing processes like injection molding and CNC milling have significant CAPEX and non-recurring engineering costs (NRE), creating financial risk. Expected revenue needs to cover, at minimum, the initial design, testing, redesign, tooling, retooling, and per unit material costs to be viable.
3D printing also changes the dynamic between product design, cost structure, MOQs, lead times/logistics, and risk. If demand changes and a product requires a redesign, additional design and tooling costs are required to pivot and satisfy customer demand. Contract manufacturers enforce high minimum order quantities (MOQs) to cover high upfront investments. As a result, companies need to hold more inventory, limiting available capital and incentive to broaden their product offering or react to market changes.
Advantages of 3D Printing Over Traditional Manufacturing
With the flexibility of 3D printing, companies can more easily manufacture a high mix of similar products, enable personalized products, or produce complex designs. Here are the three main advantages of 3D printing over traditional manufacturing:
#1 Enabling Manufacturing Agility
Tooling costs and tool testing time in traditional manufacturing processes make it very difficult to react to changes in the market or customer demand. 3D printing machines can produce a wide range of products—production level or prototypes using a broad number of polymer materials, accelerating new or existing designs into production. If the market shifts, manufacturers can quickly modify the design and move the product into production with no retooling time.
The flexibility of 3D printing processes allows multiple SKUs to be produced on a single 3D printing manufacturing line. Companies can test the market with multiple product variations, de-risking decisions on which design is produced at high volume, and enabling faster product launches.
#2 Reduced Costs and Risk
Additive manufacturing eliminates tooling costs making it economical for low volume production runs. Designs also do not need to be adapted for high volume production allowing companies to scale freely. The ease of producing a wider range of products reduces the risk for manufacturing sites. A single factory can support more customers with a high product or part mix, low volume manufacturing strategy. With greater flexibility at each site, it’s much easier to balance manufacturing capacity across multiple facilities. Additional 3D printing machines can be added to increase production capacity and throughput.
#3 Insourcing and Onshoring
3D printing lowers upfront manufacturing costs and enables greater automation and production of many different products with the same capital investment. Making manufacturing more economical allows companies to localize manufacturing, especially in countries that have high labor costs. Bringing manufacturing onshore with 3D printing provides numerous benefits:
- Greater control over quality. Bringing production onshore offers better quality control. The in-house team is directly involved in the quality control process, rather than relying on an offshore team.
- Protect your intellectual property. IP theft is a risk for companies that outsource manufacturing operations. Bringing production capabilities in-house reduces that risk.
- Faster customer response times. With 3D printing machines set up closer to the customer, companies can manufacture products on-demand. It eliminates the need to hold inventory and cuts logistic costs.
- Reduce tariff risks. There are ever-increasing tariffs on imported finished goods. Companies can tax optimize by opening manufacturing sites in the same regions as customers, eliminating import tax on final products.
The Right 3D Printing Partner Can Help You Scale
Taking an idea from development through production is difficult, expensive, and fraught with risk. Reducing cost while enabling agility and flexibility makes the process simpler and less risky. If you’re planning on using 3D printing for prototyping and/or full-scale manufacturing, working with an industry-leading manufacturing partner can give you on-demand access to a cloud-connected 3D printing smart factory. With access to modern 3D printing technologies, it’s convenient to transition from new designs and prototypes to production and scaling.
LuxCreo offers new and established companies an easy way to scale the production of new or existing products. With LuxCreo’s cloud-connected 3D printing smart factory, you can quickly get designs into production. LuxCreo gives you access to all the advantages of 3D printing over traditional manufacturing.
To learn more about leveraging the myriad advantages of 3D printing, visit our contact page or call (650) 336-0888.